A new 3D-printing technique using silicone can make accurate models of the blood vessels in your brain, enabling neurosurgeons to train with more realistic simulations before they operate, according to our recently published research.
Many neurosurgeons practice each surgery before they get into the operating room based on models of what they know about the patient’s brain. But the current models neurosurgeons use for training don’t mimic real blood vessels well. They provide unrealistic tactile feedback, lack small but important structural details and often exclude entire anatomical components that determine how each procedure will be performed. Realistic and personalized replicas of patient brains during pre-surgery simulations could reduce error in real surgical procedures.
3D printing, however, could make replicas with the soft feel and the structural accuracy surgeons need.
3D printing is typically thought of as a process that involves laying down layer after layer of melted plastic that solidifies as a self-supporting structure is built. Unfortunately, many soft materials do not melt and re-solidify the way the plastic filament that 3D printers typically employ do. Users only get one shot with soft materials like silicone – they have to be printed while in a liquid state and then irreversibly solidified.
Shaping liquids in 3D
How do you make a complex 3D shape out of a liquid without ending up with a puddle or a slumping blob?
Researchers developed a broad approach called embedded 3D printing for this purpose. With this technique, the “ink” is deposited inside a bath of a second supporting material designed to flow around the printing nozzle and trap the ink in the place right after the nozzle moves away. This allows users to create complex shapes out of liquids by holding them trapped in three-dimensional space until the time comes to solidify the printed structure. Embedded 3D printing has been effective for structuring a variety of soft materials like hydrogels, microparticles and even living cells.
However, printing with silicone has remained challenging. Liquid silicone is an oil, while most support materials are water-based. Oil and water have a high interfacial tension, which is the driving force behind why oil droplets take on circular shapes in water. This force also causes 3D-printed silicone structures to deform, even in a support medium.
Even worse, these interfacial forces drive small-diameter silicone features to break into droplets as they are being printed. A lot of research has gone into making silicone materials that can be printed without a support, but these heavy modifications also modify the properties that users care about, like how soft and stretchy the silicone is.
3D-printing silicone with AMULIT
As researchers working at the interface of soft matter physics, mechanical engineering and materials science, we decided to tackle the problem of interfacial tension by developing a support material made from silicone oil.
We reasoned that most silicone inks would be chemically similar to our silicone support material, thus dramatically reducing interfacial tension, but also different enough to remain separated when put together for 3D printing. We created many candidate support materials but found that the best approach was to make a dense emulsion of silicone oil and water. One can think about it like crystal clear mayonnaise, made from packed microdroplets of water in a continuum of silicone oil. We call this method additive manufacturing at ultra-low interfacial tension, or AMULIT.
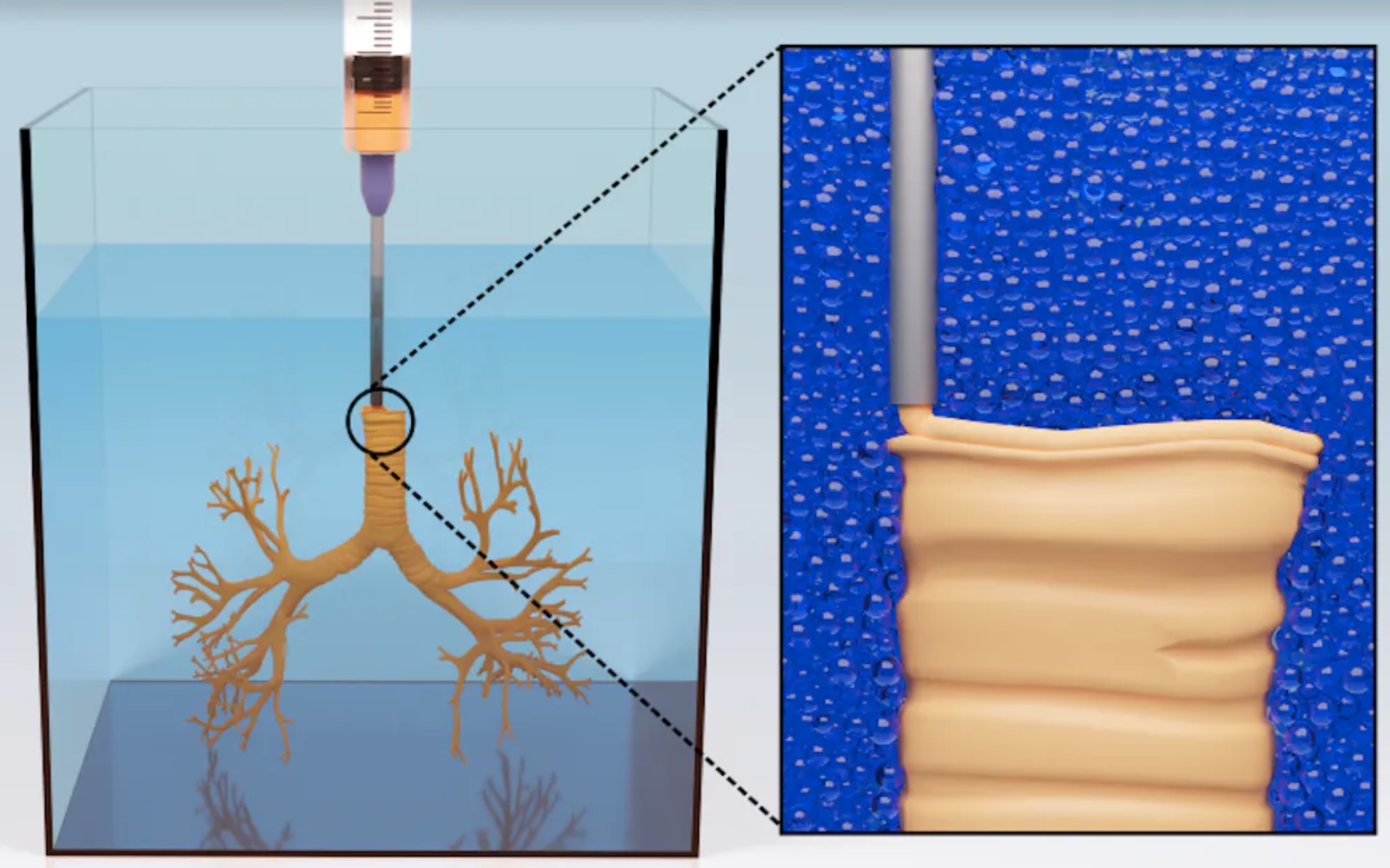
With our AMULIT support medium, we were able to print off-the-shelf silicone at high resolution, creating features as small as 8 micrometers (around 0.0003 inches) in diameter. The printed structures are as stretchy and durable as their traditionally molded counterparts.
These capabilities enabled us to 3D-print accurate models of a patient’s brain blood vessels based on a 3D scan as well as a functioning heart valve model based on average human anatomy.
3D silicone printing in health care
Silicone is a critical component of innumerable products, from everyday consumer goods like cookware and toys to advanced technologies in the electronics, aerospace and health care industries.
Silicone products are typically made by pouring or injecting liquid silicone into a mold and removing the cast after solidification. The expense and difficulty of manufacturing high-precision molds limits manufacturers to products with only a few predetermined sizes, shapes and designs. Removing delicate silicone structures from molds without damage is an additional barrier, and manufacturing defects increase when molding highly intricate structures.
Overcoming these challenges could allow for the development of advanced silicone-based technologies in the health care industry, where personalized implants or patient-specific mimics of physiological structures could transform care.
This article is republished from The Conversation under a Creative Commons license. Read the original article.